Damage to the Sealing Element. The damage to the sealing element is the main and direct cause of seal failure, and it will be further introduced as follows:
(1) Wear. Friction occurs when the sealing element slides against the metal surface, causing the sealing element to wear. Factors such as contaminants in the oil (especially metallic particles), excessively high roughness of the metal surface, and too tight installation accelerate this wear.
(2) Crevice Extrusion Deformation. The sealing element undergoes a liquefaction phenomenon under high pressure and enters the crevices of the sealing surface (as shown in Figure 1-8). The relative movement between the sealing element and the sealing groove will promote this process. Crevice extrusion leads to the complete damage of the sealing element, with surface tearing or fragmentation, and plastic deformation may also occur. Installing a sealing retainer ring can prevent the extrusion phenomenon.
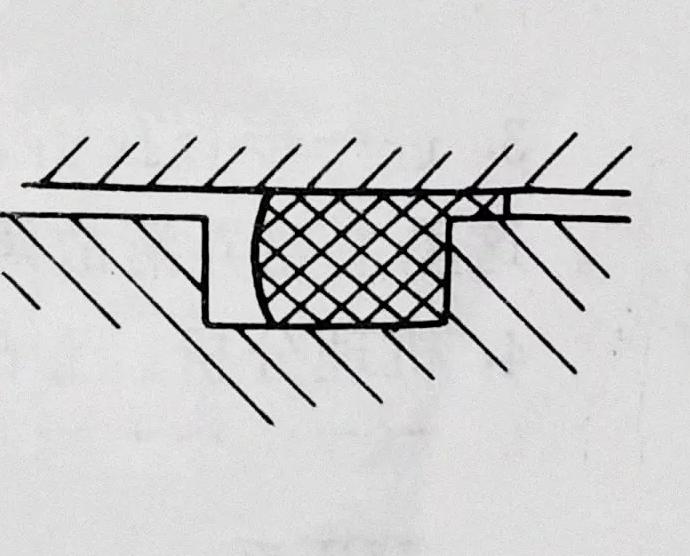
(3) Inversion. This type of failure may occur when using lip-shaped sealing elements (such as the sealing elements in a hydraulic cylinder). It is characterized by the partial extrusion of the sealing element from the groove. When the hydraulic equipment is in operation, the pressure in the sealing groove is very high. This pressure acts on the root of the sealing element, causing the root to be worn away. Then, under the action of friction force, the sealing element is turned over and extruded out of the sealing groove, cutting or breaking the sealing lip and completely damaging the sealing element.
(4) Valley Cracking. The valley part of the lip-shaped sealing element (as indicated by the arrow in Figure 1-9) is a stress concentration area and is prone to cracking when subjected to pressure shocks.
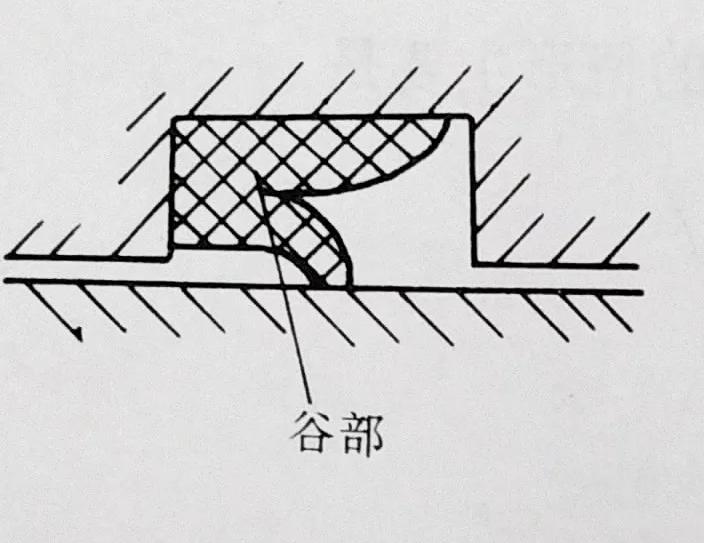
(5) Torsion. When a large frictional force occurs during the movement of the lip-shaped sealing element, a full-circle or partial torsion may occur.
(6) Uneven Wear. This is one of the main reasons for the damage of the sealing element. The eccentricity of the sealing element itself, the eccentricity of the sealing support surface, partial scratching of the mating surface between the reciprocating moving part and the sealing element, and the application of radial loads, etc., all lead to uneven wear.
(7) Material Aging. Due to a long service life, long storage time, or other reasons, the sealing element oxidizes, becomes hard and brittle, loses its elasticity, and no longer functions as a seal.